Rowan University and DMG MORI partner to advance manufacturing and education
Rowan University and DMG MORI partner to advance manufacturing and education
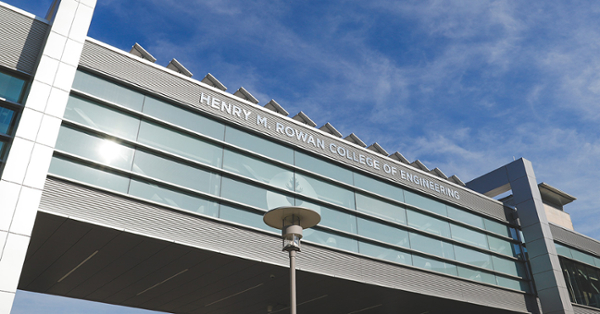
Rowan University and DMG MORI are investing in the education and training of the next generation of professionals through a partnership that provides opportunities for Rowan students. Through comprehensive degree and certification programs, the aim is to equip students and the current workforce with the skills necessary to thrive in an evolving industry. This initiative includes specialized training in advanced and additive manufacturing technologies, ensuring that graduates are well-prepared for the demands of the modern manufacturing landscape.
As part of the collaborative effort, Rowan students have opportunities to intern at DMG MORI's U.S. headquarters in Hoffman Estates, Illinois, and the company’s factory in Davis, California. These internships provide hands-on experience with the latest manufacturing technologies, fostering practical skills and industry knowledge that are essential for career success.
Rowan University and DMG MORI are well aligned in their endeavor to bring additive manufacturing and digitization to the forefront. Together, they are committed to developing and implementing end-to-end processes that streamline manufacturing for the general industry, the Department of Defense, the Department of Energy, and other sectors. The focus on minimizing carbon impact ensures that these innovations contribute to a more sustainable future for the manufacturing industry.
About DMG MORI
DMG MORI is a leading global manufacturer of high-precision machine tools and is represented in 43 countries – with 116 sales and service locations, including 17 production plants. In the “Global One Company”, more than 13,000 employees are driving the development of holistic solutions in the manufacturing industry. Our portfolio covers sustainable manufacturing solutions based on the technologies Turning, Milling, Grinding, Boring as well as Ultrasonic, Lasertec and Additive Manufacturing. With technology integration, end-to-end automation and digitization solutions we make it possible to increase productivity and resource efficiency at the same time.