Designing reusable, lightweight foams
Designing reusable, lightweight foams
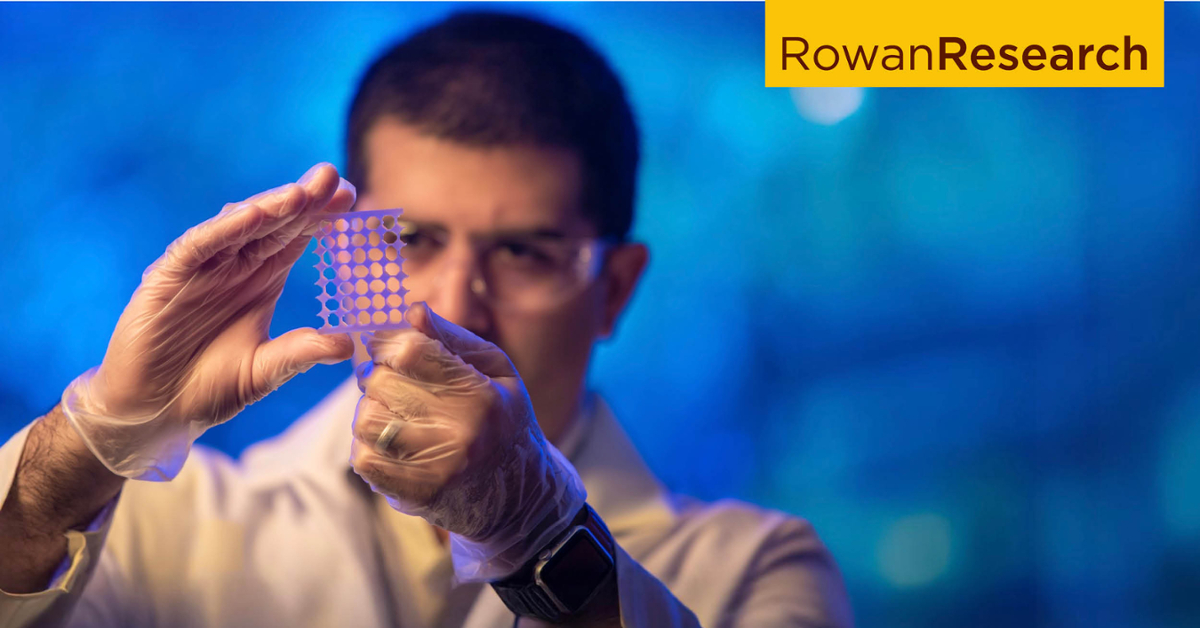
Behrad Koohbor, Ph.D.
Mechanical engineer
Areas of expertise:Mechanics of advance materials
More informationPicture a car bumper. Underneath the bumper cover is a piece of foam. In the event of a car accident, that foam absorbs energy from the crash, so the force is not transferred to the driver or passengers. But once it’s damaged from the impact of the accident, the bumper needs to be replaced. What if those energy-absorbing foams could be used multiple times and were as lightweight as possible?
This is what Behrad Koohbor, Ph.D., is studying in his lab. Koohbor, an assistant professor of mechanical engineering in the Henry M. Rowan College of Engineering, designs, tests, optimizes and manufactures energy-absorbing structures. These structures are primarily used for impact mitigation and shock absorption, with common applications from shoe soles and liners in sports helmets to aerospace and automotive industries.
Koohbor and his collaborators design flexible and lightweight materials from polymers that can withstand pressure and still retain their original shape. They then test the materials’ energy-absorbing capacities in real-world conditions.
“For a shoe sole, we know exactly how fast the midsole of a shoe is compressed and decompressed. For a football helmet liner, we know collision speeds,” Koohbor says. “We can test these materials such that the in-lab testing condition is representative of what happens during the actual use of these foams.”
The goal is to make multiuse foams that are as light and energy-absorbing as possible. Because the polymers that make up these foams are not recyclable, designing foams that can be used multiple times has environmental and cost benefits.
In the future, Koohbor hopes to add more functionalities to the materials. For example, creating foams that could also report how much longer they can be used before they need to be replaced.
To do this work, Koohbor frequently collaborates with Rowan’s Advanced Materials & Manufacturing Institute and faculty across the mechanical and chemical engineering departments. Outside of Rowan, Koohbor works with San Diego State University and the University of Lyon in France.
Koohbor’s research has been supported with funding from the National Science Foundation, the U.S. Army Research Laboratory and the New Jersey Health Foundation.
Rowan University researchers are passionate about what they do. Find more at Meet Our Researchers.