Rowan engineers join work to revolutionize material design
Rowan engineers join work to revolutionize material design
June 12, 2024
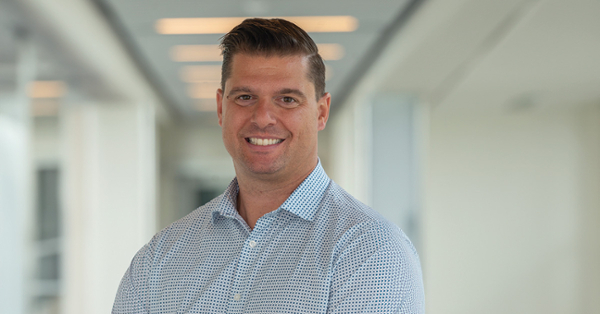
Antonios Kontsos, Ph.D.
The traditional process for developing new materials for applications such as aerospace is time- and resource-intensive.
To create a metal component found in a car, for example, a group of scientists must first devise a chemical makeup for the metal, based on input requirements like oxidation resistance. Then, mechanical engineers test the material. After that, manufacturing engineers take the metal and mold it into the form of the final product. Finally, quality and safety engineers evaluate the safety of the component.
Each step requires a separate group of scientists and engineers who often don’t directly interact with one another.
Rowan University is part of a consortium of research institutions tasked by the Defense Advanced Research Projects Agency (DARPA) to streamline this process. The goal is to create new titanium alloys in a matter of weeks that meet the standard for use in aerospace applications. The project is interdisciplinary and collaborative with teams working on alloy identification, specimen manufacturing and testing, simulations and more.
“This process encompasses revolutionary approaches to the field,” said Rowan principal investigator Antonios Kontsos, Ph.D. “I’m thrilled that my first project at Rowan is also the most challenging I have ever been involved with in my academic career.”
The Henry M. Rowan College of Engineering will be represented by the newly established Digital Engineering Hub, led by Professor Kontsos. Their role will be to collect full-field optical metrology images—high-speed and high-quality images—of the material to extract its mechanical properties using computational modeling artificial intelligence. Rowan engineers will receive the metal alloy created by the study's lead institution, the University of Virginia, and will test its mechanical properties.
During each test, the team will collect images from which researchers can predict when and how the material would fail. Researchers at other institutions on the team, including from Brown University and University of Cambridge in the United Kingdom, will perform additional measurements and apply artificial intelligence-based data modeling approaches.
“If successful, the whole process will be a first example of what is called digital engineering, in which we can, for example in this case, produce materials that meet specifications of a design constraint on demand, leveraging the digital thread between data, models and application specifications,” said Kontsos.
This novel design process can be applied to other manufacturing, aerospace, biomedical and naval applications. This project also allows students to learn cutting-edge engineering practices.
To create a metal component found in a car, for example, a group of scientists must first devise a chemical makeup for the metal, based on input requirements like oxidation resistance. Then, mechanical engineers test the material. After that, manufacturing engineers take the metal and mold it into the form of the final product. Finally, quality and safety engineers evaluate the safety of the component.
Each step requires a separate group of scientists and engineers who often don’t directly interact with one another.
Rowan University is part of a consortium of research institutions tasked by the Defense Advanced Research Projects Agency (DARPA) to streamline this process. The goal is to create new titanium alloys in a matter of weeks that meet the standard for use in aerospace applications. The project is interdisciplinary and collaborative with teams working on alloy identification, specimen manufacturing and testing, simulations and more.
“This process encompasses revolutionary approaches to the field,” said Rowan principal investigator Antonios Kontsos, Ph.D. “I’m thrilled that my first project at Rowan is also the most challenging I have ever been involved with in my academic career.”
The Henry M. Rowan College of Engineering will be represented by the newly established Digital Engineering Hub, led by Professor Kontsos. Their role will be to collect full-field optical metrology images—high-speed and high-quality images—of the material to extract its mechanical properties using computational modeling artificial intelligence. Rowan engineers will receive the metal alloy created by the study's lead institution, the University of Virginia, and will test its mechanical properties.
During each test, the team will collect images from which researchers can predict when and how the material would fail. Researchers at other institutions on the team, including from Brown University and University of Cambridge in the United Kingdom, will perform additional measurements and apply artificial intelligence-based data modeling approaches.
“If successful, the whole process will be a first example of what is called digital engineering, in which we can, for example in this case, produce materials that meet specifications of a design constraint on demand, leveraging the digital thread between data, models and application specifications,” said Kontsos.
This novel design process can be applied to other manufacturing, aerospace, biomedical and naval applications. This project also allows students to learn cutting-edge engineering practices.